Familiar with the equipment maintenance management system and master the operating procedures of each equipment to ensure the normal operation of the equipment. Carry out daily inspections of equipment operation and promptly address any issues found.
Overloading of all equipment is strictly prohibited, and operations must be carried out in strict accordance with the technical requirements of each equipment. Strengthen the daily maintenance and upkeep system of equipment, and only put it into use after confirming its normal operation and debugging. Establish and improve various equipment ledgers and equipment cards, and assign maintenance and upkeep of equipment to individuals.
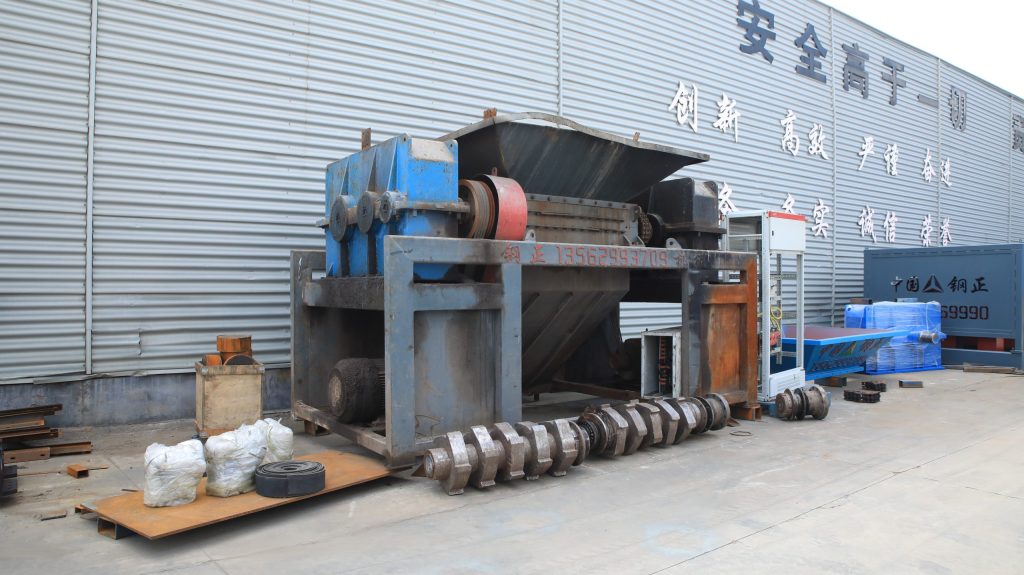
Keep the equipment clean and hygienic. For equipment that is prone to heat generation and installed in damp places, check it in a timely manner during operation. If any abnormal situation is found, stop using it immediately. Disabled and idle equipment should be managed and kept clean in the warehouse.
For special equipment, operators must hold certificates and provide professional theoretical education, training, and assessment. Violation of regulations is strictly prohibited.
Keep good records of equipment maintenance and repair, and assign responsibility to individuals. If any problems are found during the next use of the repaired equipment that affect production, the maintenance personnel shall bear the responsibility.
Due to operational errors resulting in equipment accidents and damage, operators should be compensated at 80% of the equipment maintenance cost and ordered to be laid off. The principles and requirements of mechanical equipment maintenance system are to ensure that mechanical equipment is in good technical condition, can be put into operation at any time, reduce downtime due to faults, improve mechanical integrity and utilization, reduce mechanical wear, extend mechanical service life, reduce mechanical operation and maintenance costs, ensure safe production, and strengthen maintenance work on mechanical equipment. Mechanical maintenance follows the principle of “equal emphasis on maintenance and prevention”, achieving regular and mandatory maintenance, correctly handling the relationship between use, maintenance, and repair, and not allowing the use without maintenance or repair without maintenance. Each team shall carry out maintenance work on various types of machinery in accordance with the mechanical maintenance regulations and categories, and shall not delay without reason. In special circumstances, approval from the responsible specialist is required before extending the maintenance, but generally not exceeding half of the prescribed maintenance interval. The maintenance of machinery must ensure quality, and be carried out item by item according to the prescribed items and requirements, without any omissions or omissions. The maintenance items, maintenance quality, and problems discovered during maintenance should be recorded and reported to the department’s specialist.
Maintenance personnel and departments should achieve “three inspections and one handover (self inspection, mutual inspection, dedicated inspection, and one-time handover qualification)”, constantly summarize maintenance experience, and improve maintenance quality. The Asset Management Department regularly supervises and inspects the mechanical maintenance of each unit, conducts regular or irregular spot checks on maintenance quality, and rewards and punishes excellence. The implementation and supervision of maintenance operations: Mechanical maintenance adheres to the promotion of the “cross” operation method with “cleaning, lubrication, adjustment, fastening, and anti-corrosion” as the main content, implements routine and regular maintenance systems, and strictly follows the cycle and inspection maintenance items specified in the user manual. Routine maintenance is the cleaning and inspection carried out before, after, and during the operation of machinery, mainly checking the condition of critical and vulnerable components (such as mechanical safety devices), coolant, lubricants, fuel levels, instrument indicators, etc. Routine maintenance is completed by the operator themselves and the ‘Mechanical Routine Maintenance Record’ is carefully filled out.
First level maintenance: generally carry out cleaning, fastening, and lubrication operations, and partially adjust operations to maintain the mechanical integrity and technical condition. The asset management personnel of the user unit shall issue a “Mechanical Equipment Maintenance and Lubrication Notice” according to the maintenance plan and issue it to the operation team. The operator shall complete it himself, and the operation team leader shall inspect and supervise it.
Second level maintenance: includes all the contents of first level maintenance, with inspection and adjustment as the center, to maintain the good working performance of various mechanical assemblies, mechanisms, and parts. The “Mechanical Equipment Maintenance and Lubrication Notice” shall be issued by the asset management personnel of the user unit and issued to the operation team. It is mainly completed by the operator himself. If the operator encounters difficulties in completing it, he can entrust the repair department for inspection and supervision by the asset administrator and operation team leader of the user unit. Other maintenance. Seasonal maintenance: The main content is to replace lubricating oil and fuel suitable for the season, take anti freezing measures, and increase anti freezing facilities. Organized and arranged by the user department, inspected and supervised by the operation team leader.
Comments are closed